1. 서 론
산소환원반응은 전기화학적 에너지 변환 및 저장 소자 의 핵심적인 양극 반응이며, 특히 연료전지 및 금속 공 기 전지와 같은 높은 에너지 밀도를 갖는 소자에서 이 용되고 있다. 하지만, 산소환원반응은 음극에서 발생하는 반응과 비교하여 더 복잡하고 느린 반응이기 때문에 산 소환원반응을 촉진시킬 수 있는 합리적인 촉매 설계를 통하여 향상된 전기화학반응을 이끌어내야 한다.1-4) 일반 적으로, 산소환원반응의 더딘 속도를 향상시키는 것으로 백금계 전기화학 촉매가 가장 많이 사용되고 있지만, 백 금계 촉매의 경우 높은 가격, 희소성, 높은 과전압 손실 및 낮은 안정성이라는 치명적인 문제점을 갖고 있다.5-7) 이러한 문제점을 해결하기 위해 최근 백금을 대체할 수 있는 비백금계 소재에 대한 연구가 활발히 진행중이며, 우 수한 물리적 및 화학적 안정성과 함께 높은 전기전도도 를 갖는 탄소 소재가 많은 관심을 끌고 있다. 탄소 소 재로는 탄소나노튜브, 그래핀, 흑연, 탄소나노섬유 등이 있으며, 이들 중 탄소나노섬유는 우수한 물리적 및 화 학적 안정성, 높은 전기전도도(102S cm−1) 및 넓은 비표 면적(> 350 m2 g−1)의 특성을 지니고 있을 뿐만 아니라 1 차원 구조의 섬유가 네트워크 구조로 이루어져 있어 전 자 이동을 효율적으로 전달 할 수 있다.8,9) 이러한 탄소 소재에 황, 불소, 인, 질소 등과 같은 이종원소들을 도 핑하여 산소환원반응을 향상시킬 수 있으며, 특히 이종 원소 중 질소 도핑된 탄소는 기존의 탄소와 비교하여 향 상된 산소환원반응 활성도를 보이는데 이는 효율적인 산 소 흡착과 함께 산소의 환원을 돕기 때문이다.10-13) 하지 만, 질소 도핑된 탄소는 여전히 백금계 촉매와 비교하 여 산소환원반응 활성도가 상대적으로 낮게 나타난다. 이 는 탄소에 도핑 될 수 있는 질소의 양이 제한적이기 때 문이다. 이러한 문제점을 극복할 수 있는 방법은 탄소 소재에 탄화물, 질화물, 황화물 등을 복합화하여 산소환 원반응 활성도를 향상시키는 것이다. 탄화물 중 하나인 탄화철은 우수한 산소 흡착력을 갖고 있어 질소 도핑된 탄소의 부족한 촉매 활성 면적을 향상시킬 수 있다.14-16) 따라서, 질소 도핑된 탄소나노섬유에 탄화철의 복합화는 산소환원반응용 비백금계 촉매로서 적합할 것으로 판단 된다.
본 연구에서는 전기방사법, 전구체 코팅 및 탄화 과정 을 통하여 탄화철을 내재한 질소 도핑된 탄소나노섬유 를 제조하였다. 질소 도핑 및 탄화철을 탄소나노섬유에 도 입하기 위하여 질소 함량이 높은 iron(II) phthalocyanine 를 전구체로 활용하였으며, 전구체 코팅시 이들의 양을 체계적으로 조절하여 탄화철이 내재된 질소 도핑된 탄 소나노섬유를 최적화하였다. 제조된 샘플들은 산소환원반 응용 촉매로 사용되었고, 촉매의 활성도 및 전기화학적 안정성을 규명하였다.
2. 실험 방법
탄화철이 내재된 질소 도핑된 탄소나노섬유를 산소환 응반응용 비귀금속 촉매로 이용하기 위하여 전기방사법, 전구체 코팅 및 탄화를 이용하여 다음과 같이 제조하였 다. 먼저, N, N-Dimethylformamide(DMF, Aldrich) 용 매에 탄소 전구체인 polyacrylonitrile(PAN, Mw= 150,000 g mol−1, Aldrich)을 3시간 동안 용해하였다. 그리고 나서 용액을 10 mL 플라스틱 주사기에 옮긴 후 23게이지를 갖는 스테인리스 바늘을 장착했다. 공급기에 용액이 담 긴 주사기를 장착하고 알루미늄 포집판과 바늘 팁의 거 리를 15 cm로 설치하였다. 0.03 mL h−1로 공급기의 주입 속도를 유지한 채 직류전원 공급기를 이용하여 전압을 13 kV로 유지하면서 전기방사를 진행하였다. 전기방사 후 얻어지는 PAN기반 나노섬유에 탄화철을 내부에 생성하 기 위해 전구체 코팅을 다음과 같이 진행하였다. 전구 체인 iron(II) phthalocyanine(FeC32H16N8, Aldrich)을 Ethanol( C2H6O, Aldrich) 용매 대비 0.5 wt%, 1 wt% 및 2 wt%로 용해하였다. 그 다음, 얻어지는 나노섬유를 준비 된 용액과 함께 1시간 동안 교반 시킨 후 오븐에서 50 °C 로 건조하였고 얻어지는 샘플들은 280 °C에서 2시간 동 안 안정화를 시킨 후 고순도(99.999 %) 질소 분위기에서 800 °C 탄화 과정을 통하여 탄화철이 내재된 질소 도핑 된 탄소나노섬유를 제조하였다. 따라서, 본 논문에서는 철 전구체를 0.5 wt%, 1 wt% 및 2 wt%로 조절한 탄화철 이 내재된 질소 도핑된 탄소나노섬유를 Fe3C-embedded N doped CNF-0.5, Fe3C-embedded N doped CNF-1 및 Fe3C-embedded N doped CNF-2로 각각 언급될 것 이다. 모든 샘플의 구조 및 형태 분석은 전계방사형 주 사전자 현미경(FESEM, Hitachi S-4800)과 투과전자현미 경(MULTI/TEM; Tecnai G2, KBSI Gwangju Center) 이 용하였다. 또한, 그들의 결정구조를 확인하기위해 X-선 회절 분석(X-ray diffraction, XRD, Rigaku Rint 2500) 을 이용하였고, X-선 광전자 주사법(X-ray photo-electron spectroscopy, XPS, ESCALAB 250 equipped with an Al kα X-ray source)을 이용하여 표면에서의 화학적 결 합상태를 규명하였다. Fe3C-embedded N doped CNF의 산소환원반응 촉매 특성을 평가하기 위하여 potentiostat/ galvanostat(Ecochemie Autolab PGST302N, Netherlands) 과 함께 삼전극 시스템을 이용하여 전기화학적 분석을 진행하였다. 삼전극 시스템은 작업전극(glassy carbon electrode, area = 0.0706 cm2), 상대전극(Pt guaze) 및 기준전 극(Ag/AgCl, saturated KCl)으로 구성되어 있다. Fe3Cembedded N doped CNF 는 Nafion(Aldrich)과 8:2비율 의 무게비로 촉매잉크를 제조하여 3일간 고르게 분산시 켰다. 제조된 촉매잉크를 작업전극 위에 고르게 코팅한 후 오븐에서 50 °C로 건조하였고, 전해질은 0.1 M 수산 화칼륨(Potassium hydroxide, KOH)용액을 사용하였다. Fe3C-embedded N doped CNF의 산소환원반응 특성은 산소가스가 충분히 공급된 전해질내에서 선형 이동 전 압 곡선(linear sweep voltammogram, LSV)을 이용하여 측정하였다. 이 때, 5 mV s−1의 scan rate으로 −0.7 V에 서 0.2 V까지의 전압 범위에서 1,600 rpm 의 회전속도 로 선형이동전압곡선을 측정하였다. 더 나아가서, 제조된 촉매들의 전기화학적 안정성을 분석하기 위하여 순환전 압-전류측정법(Cyclic Voltammetry, CV)을 −0.9 V에서 0.4 V까지인(vs. Ag/AgCl) 전압 범위에서 50 mV s−1의 scan rate으로 3,000회 동안 진행한 후 선형 이동 전압 곡선 을 측정하여 초기 대비 촉매의 안정성을 평가하였다.
3. 결과 및 고찰
Fig. 1은 Fe3C-embedded N doped CNF-0.5 [Fig. (a, d)], Fe3C-embedded N doped CNF-1 [Fig. (b, e)] 및 Fe3C-embedded N doped CNF-2 [Fig. (c, f)]의 전계방 사형 주사전자 현미경 이미지를 나타낸다. Fig. 1에서 보 여지는 것처럼, 모든 샘플은 매끈한 표면을 갖는 탄소 나노섬유의 형상을 보이며, 균일하게 제조되었다. 평균 직 경의 경우 Fig. 1(a, d)는 약 252.03-289.87 nm, Fig. 1(b, e)의 경우 약 248.84-275.46 nm 및 Fig. 1(c, f)의 경우 254.74-291.32 nm로 관찰되었다. 그러나 Fe3C-embedded N doped CNF-2의 경우 탄소나노섬유 표면에 응집된 탄 화철이 관찰되는데, 이는 전구체 코팅과정에서 철 전구 체의 양이 과잉 되었기 때문으로 판단된다. 제조된 샘 플들의 형상과 구조적인 특성을 더 자세히 분석하기 위 해 투과 전자 현미경 분석을 진행하였다.
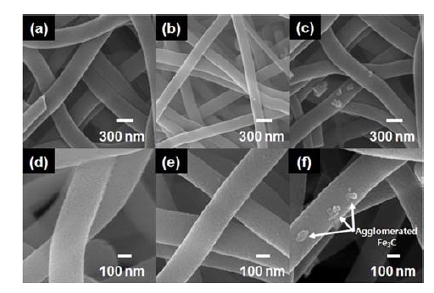
Fig. 1
FESEM images of (a, d) Fe3C-embedded N doped CNF-0.5, (b, e) Fe3C-embedded N doped CNF-1, and (c, f) Fe3C-embedded N doped CNF-2.
Fig. 2(a)는 Fe3C-embedded N doped CNF-0.5, Fig. 2(b)는 Fe3C-embedded N doped CNF-1 및 Fig. 2(c)는 Fe3C-embedded N doped CNF-2의 투과전자현미경 이미 지를 나타낸다. Fig. 2(a)의 경우, 제조된 샘플은 상대적 으로 밝은 명암을 갖는 탄소나노섬유와 어두운 명암을 갖는 탄화철로 구분된다. 특히, 탄화철이 탄소나노섬유 내 부에 드물게 분포하는 것을 확인 할 수 있다. 이것은 전 구체 코팅과정에서 철 전구체의 양이 적었기 때문이다. Fe3C-embedded N doped CNF-1의 경우, 탄화철이 탄소 나노섬유 내부에 잘 분산되고 상대적으로 적은 양의 탄 화철이 응집하는 것을 Fig. 2(b)에서 확인 할 수 있다. 또한, 탄화철의 입자크기는 12-19 nm로 관찰되며 잘 분 산된 나노크기의 탄화철은 전기화학적 촉매 활성 면적 을 더 많이 제공하여 산소환원반응 동안 전기화학적 촉 매 활성도를 향상시킬 수 있다. 그러나, Fig. 2(c)의 경 우는 탄소나노섬유 내부에 응집된 탄화철이 관찰되었다. 이것은 전구체 코팅을 진행하였을 때 철 전구체 양이 과 잉 되었기 때문이다. 응집된 탄화철은 전기화학적 촉매 활성면적을 줄여 산소환원반응동안 전기화학적 촉매 활 성도를 줄일 수 있다.
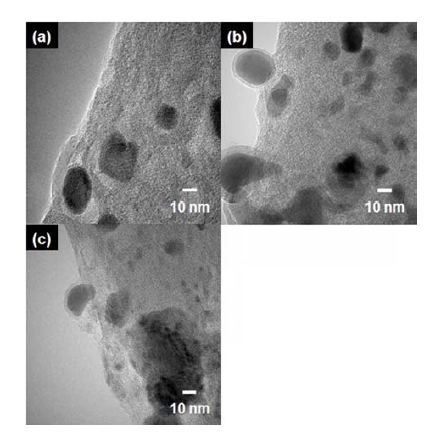
Fig. 2
TEM images of (a) Fe3C-embedded N doped CNF-0.5, (b) Fe3C-embedded N doped CNF-1, and (c) Fe3C-embedded N doped CNF-2.
Fig. 3은 Fe3C-embedded N doped CNF-0.5, Fe3Cembedded N doped CNF-1 및 Fe3C-embedded N doped CNF-2의 X-선 회절분석 결과를 나타낸다. 모든 샘플은 약 25o에서 흑연의 (002)면에 대한 회절 피크가 나타난 다. 또한, 탄화철 상의 (031)면에 상응하는 45.0o의 주 회 절 피크가 관찰되고, 이는 사방정계(JCPDS card No. 35- 0772)를 나타낸다. 탄화철의 입자크기는 Scherrer equation 을 이용하여 다음과 같이 계산할 수 있다.17,18)
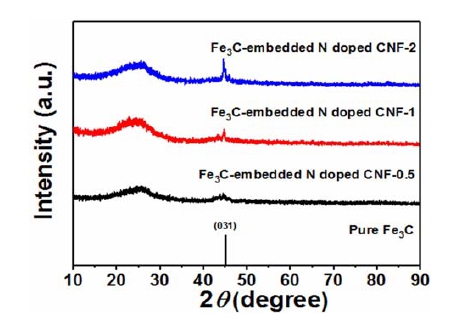
Fig. 3
XRD data of Fe3C-embedded N doped CNF-0.5, Fe3Cembedded N doped CNF-1, and Fe3C-embedded N doped CNF-2.
이 식에서 λ는 X-선 파장, β는 반치폭, θ는 Bragg angle을 의미한다. 위 공식을 이용하여 탄화철의 입자 크 기를 회절 피크들인 (031)면을 이용하여 계산하였다. Fe3Cembedded N doped CNF-0.5, Fe3C-embedded N doped CNF-1 및 Fe3C-embedded N doped CNF-2의 탄화철 입 자의 평균 크기는 각각 약 10.4 nm, 14.7 nm 및 21.5 nm임을 확인하였고, 이는 투과 전자 현미경 분석과 일 치함을 알 수 있다.
Fig. 4는 Fe3C-embedded N doped CNF-1의 화학적 결합상태를 규명하기 위하여 XPS 스펙트럼을 나타내었 고, 모든 스펙트럼 피크들은 C 1s line(284.5 eV)을 이용 하여 보정하였다. Fig. 4(a)의 경우 C 1s 광전자에 대한 XPS 피크들이 284.5 eV, 286.1 eV, 287.5 eV 및 288.8 eV에서 관찰되었고, 이는 각각 C-C, C-O, C=O 및 OC= O를 의미한다. 더욱이 제조된 Fe3C-embedded N doped CNF-1의 질소 도핑을 분석하기 위하여 N 1s 피크들에 대한 스펙트럼을 Fig. 4(b)에 나타내었다. N 1s 광전자 에 대한 XPS 피크들은 398.4 ± 0.3 eV(pyridinic-N), 400.0 ± 0.3 eV(pyrrolic-N), 401.0 ± 0.3 eV(graphitic-N) 및 403.0 ± 0.3 eV(pyridinic-N oxide)와 같은 4개의 주요 피크로 나눌 수 있다. 특히 탄소 기지에 p-전자를 제공할 수 있 는 pyridinic-N의 존재는 탄소의 촉매 활성을 위한 전자 공여 특성을 향상시킨다.19-21) 따라서, 탄소지지체에 높은 비율의 pyridinic-N은 산소환원반응용 촉매 성능을 향상 시킬 수 있다. Fig. 4(c)의 경우 Fe3C를 의미하는 Fe 2p 광전자에 대한 XPS 피크들이 712.9 eV 및 727.6 eV에 서 관찰되었으며, 720.1 eV에서 위성(satellite) 피크가 나 타난다. 탄화철의 격자는 3개의 철 원자 중앙에 탄소가 위치하게 되는데 이러한 결정 구조는 철 원자의 활성화 를 도우며 이를 통해 산소 흡착력의 향상으로 효과적인 산소환원반응을 이끌 수 있다.16)
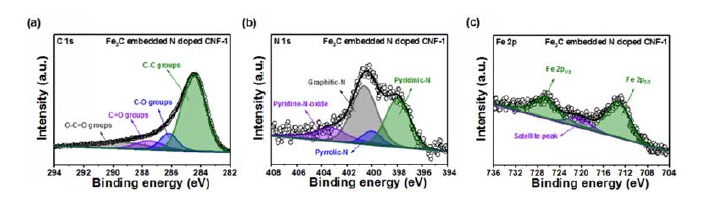
Fig. 4
XPS data of Fe3C-embedded N doped CNF-1 for (a) carbon, (b) nitrogen, and (c) iron species, respectively.
Fig. 5(a)는 탄소나노섬유, Fe3C-embedded N doped CNF-0.5, Fe3C-embedded N doped CNF-1 및 Fe3Cembedded N doped CNF-2의 전기화학적 특성을 분석한 선형 이동 전압 곡선을 나타낸 것이고, 이는 전극 회전 속도를 1,600rpm으로 유지하며 측정하였다. 일반적으로, 높 은 전압에서 낮은 전압으로 측정이 진행될수록 전류 값 이 떨어지는데 이는 산소환원반응이 일어남을 의미하고, 촉매의 산소환원반응 활성도를 분석하는 방법으로는 전 류 값이 하강하기 시작하는 지점인 반응시작 전위(on-set potential)와 전류 값이 하강하기 시작하는 지점과 종료 하는 지점 사이에 중간 지점의 전압 인 반파전위(halfwave potential)를 이용한다. Fe3C-embedded N doped CNF-0.5, Fe3C-embedded N doped CNF-1 및 Fe3Cembedded N doped CNF-2의 반응시작 전위는 각각 −0.25 V, −0.18 V 및 −0.30 V의 값을 나타내며, 반파 전 위는 각각 −0.34 V, −0.29 V 및 −0.39 V의 값을 나타낸 다. 그러나, 탄소나노섬유의 경우 거의 평행한 전류 값 이 나타나는데, 이는 산소환원반응이 발생하지 않았음을 의미한다. 더욱이 산소환원반응 과정을 분석하기 위하여 전자 이동 수 (n)를 분석하였고, 이는 Koutecky-Levich (K-L) 방정식을 이용하였다.12,16)
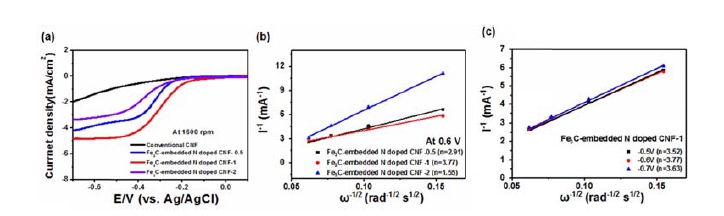
Fig. 5
(a) LSV curves of conventional CNF, Fe3C-embedded N doped CNF-0.5, Fe3C-embedded N doped CNF-1, and Fe3C-embedded N doped CNF-2 at a rotating speed of 1,600 rpm in an O2-saturated 0.1 M KOH electrolyte, (b) Koutecky-Levich plots of Fe3C-embedded N doped CNF-0.5, Fe3C-embedded N doped CNF-1, and Fe3C-embedded N doped CNF-2 at −0.6 V, and (c) Koutecky-Levich plots of Fe3C-embedded N doped CNF-1 at −0.5 V, −0.6 V, and −0.7 V.
이 식에서 j는 전류밀도, jk는 전극의 반응 전류밀도, jd는 확산 전류밀도, n은 전자 이동 수, F는 패러데이 상 수(F = 96,485 C mol−1), k는 전자 이동 계수, CO는 전해 질 내에서 산소 농도(CO= 1.2 × 10−3 mol L−1), DO는 전해 질 내에서 산소 확산 계수(DO= 1.9 × 10−5cm2 s−1), v는 전해질의 점도(v = 1 × 10−2cm2 s−1), ω는 회전 각속도(ω = 2πN, N은 선형 회전 속도)를 의미한다. Fig. 5(b)는 모 든 샘플들의 −0.6 V에서 K-L 방정식을 이용하여 계산된 전자 이동 수(n)이며, 전자 이동 수(n)의 경우, Fe3Cembedded N doped CNF-0.5는 2.91, Fe3C-embedded N doped CNF-1은 3.77 및 Fe3C-embedded N doped CNF-2는 1.55로 관찰되었다. 또한, Fe3C-embedded N doped CNF-1의 전압에 따른 전자 이동 수(n) 유지율을 Fig. 5(c)에 나타내었다. 전자 이동 수의 경우 −0.5 V, −0.6 V 및 −0.7 V에서 각각 3.52, 3.77 및 3.63으로 관찰되었 고, Fe3C-embedded N doped CNF-1의 경우 이론적으로 최대 반응인 4-전자 반응에 거의 근접한다. 따라서 모든 샘플 중 Fe3C-embedded N doped CNF-1은 향상된 반 응시작 전위, 반파 전위, 전자 이동 수 및 유지율을 갖 고, 이는 우수한 산소환원능력을 의미한다. Fe3C-embedded N doped CNF-1의 향상된 산소환원반응 활성도는 두 가 지 주요 영향으로 분석 할 수 있다. 첫째로, 탄소 내부 에 잘 분산된 나노 탄화철이 산소 흡착력을 향상시켰기 때문이다. 둘째로, 탄소 내부에 높은 비율의 pyridinic-N 은 전자 공여 특성을 향상시켜 산소환원반응 활성도를 증가시켰기 때문이다.
Fig. 6(a-c)는 전기화학적 안정성 평가를 진행하기 위 하여 순환전압전류법을 3,000회 진행 한 뒤에 다시 선 형 이동 전압 곡선을 측정하여 Fe3C-embedded N doped CNF-0.5, Fe3C-embedded N doped CNF-1 및 Fe3Cembedded N doped CNF-2의 초기 대비 전기화학적 안 정성을 평가한 것이다. 반파 전위의 감소 값은 각각 17 mV, 8 mV 및 28 mV을 나타냈으며, 이는 Fe3C-embedded N doped CNF-1이 모든 샘플 중 촉매 안정성이 가장 높 음을 의미한다. 이렇게 전기화학적 안정성이 향상된 이유 는 질소 도핑된 탄소나노섬유가 내부의 탄화철을 부식으 로부터 막는 보호층으로 작용했기 때문으로 판단된다.15)
4. 결 론
본 연구에서는 산소환원반응용 비귀금속 촉매로 이용 하기 위하여 탄화철을 내재한 질소 도핑된 탄소나노섬 유를 전구체 코팅법 및 탄화를 통해 성공적으로 제조하 였다. 탄소나노섬유, Fe3C-embedded N doped CNF-0.5 및 Fe3C-embedded N doped CNF-2와 비교하여, Fe3Cembedded N doped CNF-1는 −0.18 V의 반응시작 전위, −0.29 V의 반파 전위로 향상된 산소환원반응 특성을 보 이며 특히 3.77의 산소 이동 수로 일반적으로 최대 전 자 이동 수인 4에 거의 근접한다. 이렇게 향상된 전기 화학적 특성을 보이는 이유는 첫째로, 산소 흡착력을 향 상시키는 탄화철이 탄소나노섬유 내부에 나노크기로 고 르게 분산되었고, 이는 전기화학적 촉매 활성 면적을 향 상시켰기 때문이다. 둘째로, 질소 도핑 중 pyridinic-N의 존재는 촉매 활성을 위한 전자 공여 특성을 향상시켰기 때문이다. 또한, 초기 대비 전기화학적 안정성을 평가하 였을 때 8 mV의 가장 적은 반파 전위 감소 값을 보이 는데, 이는 우수한 전기화학적 안정성을 의미한다. 이렇 게 전기화학적 안정성이 향상된 이유는 질소 도핑된 탄 소나노섬유가 탄화철의 부식을 막는 보호층으로 작용하 였기 때문이다. 따라서, 낮은 산소환원반응 활성도를 갖 는 탄소나노섬유와 값비싼 백금 촉매를 대체할 수 있는 탄화철을 내재한 질소 도핑된 탄소나노섬유는 산소환원 반응용 비귀금속 촉매로 유망할 전망이다.