1. 서 론
기계적 에너지와 전기에너지 간의 상호 변환이 가능한 압전 세라믹스는 각종 물리센서 및 액츄에이터 소자의 핵심 소재로 사용되고 있다.1,2,3,4) 상용화된 압전 세라믹스는 대부분 Pb(Zr,Ti)O3 (PZT) 기반의 조성을 가지며 우수한 압전 특성을 나타내지만, 유해한 납의 함량이 60 % 이상 포함되어 있어 사용 규제 대상 소재로 자주 언급되고 있다.5,6,7,8) 이로 인해 비납계 압전 세라믹스 소재 개발 연구가 활발히 진행되고 있으며, 다양한 비납계 압전 세라믹스 중 (K,Na)NbO3 (KNN) 기반 세라믹스는 준수한 압전특성과 높은 큐리온도를 나타내어 주목을 받았으며,9,10,11) PZT기반 세라믹스 수준으로 압전특성을 향상시키기 위한 연구들이 지속되고 있다.12,13) 순수KNN세라믹스의 rhombohedral-orthorhombic (R-O) 상전이 온도는 약 -120 °C, orthorhombic-tetragonal (O-T) 상전이 온도는 약 200 °C이며, 압전특성 향상을 위한 대부분의 연구들은 O-T 상전이 온도를 상온 부근으로 낮추거나 R-T 상경계 조성을 설계하는 방향으로 진행되었다.12,14) 특히, R-O와 O-T 상전이 온도를 상온 부근에서 만나게 함으로써 형성되는 R-T 상경계 조성에서 PZT 기반 소재에 버금가는 매우 높은 압전특성이 나타난다고 보고되었다.15,16,17,18) KNN 기반 세라믹스의 R-T 상경계 형성을 위해 주로 Li+, Sb5+, Ba2+, Ca2+, Zr4+, Hf4+ 등의 이온 도핑 연구와 페로브스카이트 구조의 BaZrO3, SrTiO3 등을 고용시키는 연구들이 진행되었다.19,20,21,22,23,24,25,26,27,28,29,30)
R-T 상경계 조성을 갖는 KNN기반 세라믹스의 경우 결정립 크기가 1 µm 미만일 때에는 R상으로 존재하고, 결정립 크기가 1 µm보다 커지게 되면 R-T 상경계가 형성된다고 보고되었다.31) 또한, 수십 µm 크기의 비정상 결정립 주변에 수백 nm 크기의 결정립들이 혼재되어 있는 미세구조가 형성될 때 압전특성과 온도 안정성이 향상된다고 알려져 있다.32,33) 하지만, 과도한 입성장이 일어나게 되면 오히려 상온에서 R-T 상경계가 O-T 상경계로 변화하면서 압전특성이 저하된다고 보고되었으며,32) 우수한 압전성능 확보를 위해서는 세라믹 소결체의 미세구조 제어가 매우 중요하다.34,35)
일반적인 소결 공정에서 세라믹스 소재의 미세구조 제어를 위한 가장 기본적인 방법은 소결 온도를 변화시키는 것이다. KNN 기반 세라믹스의 경우 고온 소결 공정에서 알칼리 원소의 높은 휘발성으로 인해 밀도가 감소하고 전기적 특성이 저하되는 문제점이 보고되었다.23,36,37,38) 또한, 복잡한 조성의 KNN 기반 세라믹스에서 과도한 알칼리 원소의 휘발은 조성 불균일을 초래하여 압전특성의 재현성을 저하시키는 문제점이 있어, 소결 시 알칼리 원소 휘발을 억제하는 것은 매우 중요하다.39,40,41) KNN 기반 세라믹스의 알칼리 원소 휘발을 억제하면서 치밀화된 미세구조를 확보하기 위한 방안으로 스파크 플라즈마 소결, 가압 소결, two-step 소결 등과 같은 개선된 소결 공정들이 시도되었다.23,42,43,44,45,46,47) Two-step 소결법의 경우, 1단계에서 기존의 일반적인 소결온도보다 20~100 °C 정도 높은 온도로 승온한 후 0~1시간의 짧은 시간 동안 소결하여 초기 입자의 성장과 치밀화를 유도하고, 2단계에서는 기존 소결온도보다 약 100 °C 정도 낮은 온도에서 장시간 소결되어 기공이 제거되면서 높은 밀도를 얻을 수 있다고 보고되었다.23,48)
본 연구에서는 상온에서 R-T 상경계 구조를 나타내는 KNN 기반 소재로서 0.96(K0.456Na0.536)Nb0.95Sb0.05-0.04Bi0.5(Na0.82K0.18)0.5ZrO3 세라믹스를 선정하여 일반적인 one-step 소결 및 two-step 소결 공정을 도입하였을 경우 미세구조와 압전특성이 어떻게 변화하는지 알아보고자 하였다. One-step 소결 공정에서는 소결 온도를 제어 변수로 설정하였고, two-step 소결 공정에서는 1단계 유지 시간을 제어 변수로 설정하였다. 각 소결 공정에 의해 제조된 시편들의 구조 분석과 전기적 특성 분석을 수행한 후, 압전 소자 적용 시 각 시편들의 미세구조 및 압전특성이 미치는 영향을 알아보기 위해 압전-자왜 자기전기 복합체 소자를 제작하여 자기장-전기장 변환 성능을 평가하였다.
2. 실험 방법
0.96(K0.456Na0.536)Nb0.95Sb0.05-0.04Bi0.5(Na0.82K0.18)0.5ZrO3 (KNNS-BNKZ) 조성 세라믹 분말은 K2CO3 (99 %), Na2CO3 (99 %), Nb2O5 (99.9 %), Sb2O5 (99.9 %), Bi2O3 (99.9 %), ZrO2 (98 %) 원료 분말(고순도화학)을 이용한 고상합성법으로 준비되었다. 원료 분말에 존재하는 수화물 상의 제거를 위해 K2CO3와 Na2CO3분말은 400 °C의 진공에서 24시간 동안 열처리되었다. 이후, 각 원료 분말은 조성에 맞게 칭량된 후 지르코니아볼(YSZ, SciLab)과 무수에탄올(99.9 %, 삼전순약공업)이 담긴 폴리에틸렌 용기안에서 일반적인 볼밀 공정을 통해 24시간 동안 분쇄 및 혼합되었다. 혼합된 분말은 950 °C에서 6시간 동안 하소되었으며, 하소된 분말은 다시 동일한 볼밀 공정을 통해 24시간 동안 재분쇄된 후 100 MPa의 압력으로 일축 가압되어 디스크 형태로 성형되었다. 이후 성형체들은 아래의 one-step 및 two- step 소결 조건에 따라 소결되었다.
1) One-step 소결: 4 °C/min 속도로 상온에서 소결 온도(1,055, 1,070, 1,085, 1,100, 1,115 °C)까지 승온 후 소결 온도에서 4시간 동안 소결 ⟶ 6 °C/min 속도로 상온까지 냉각.
2) Two-step 소결: 4 °C/min 속도로 상온에서 1,130 °C까지 승온 후 1,130 °C에서 30분 또는 60분 동안 유지 ⟶ 10 °C/min 속도로 1,070 °C까지 냉각 후 1,070 °C에서 4시간 동안 소결 ⟶ 6 °C/min 속도로 상온까지 냉각.
소결된 시편들의 물성 평가를 위해 시편 양면에 Ag 페이스트를 도포하여 600 °C에서 30분 동안 전극 소결하였으며, 이후 전극이 형성된 시편들을 상온의 실리콘 오일에서 30분 동안 4 kV/mm의 직류 전기장을 인가하여 분극시켰다.
KNNS-BNKZ 세라믹스의 상과 미세구조는 X-ray diffraction (XRD, MiniFlex, Rigaku, Japan)과 scanning electron microscopy (SEM, SNE-4500M, SEC, Korea)에 의해 분석되었다. 소결체의 압전 및 유전 특성은 d33 미터기(YE2730A, Sinocera piezotronics, China)와 impedance analyzer (IM3570, Hioki, Japan)에 의해 측정되었다. 자기전기(magnetoelectric) 특성 평가를 위해 분극된 소결체의 상하부에 90 µm 두께의 Metglas (2605SA1, Metglas Inc., USA)층을 에폭시 접착제(DP460, 3M company, USA)를 사용하여 부착함으로써 자기전기 적층 복합체를 제작하였다. 직류 자기장 세기(HDC)에 따른 자기전기 전압계수(magnetoelectric voltage coefficient)는 Helmholtz 코일, 전자석 및 lock-in amplifier (SR860, Stanford Research Systems, USA)로 구성된 장치에 의해 측정되었다.
3. 결과 및 고찰
다양한 온도에서 4시간 동안 소결된one-step 소결체의 표면 SEM 미세구조를 Fig. 1(a-e)에 나타내었다. 1,055 °C와 1,070 °C의 온도에서 소결된 시편들의 경우 Fig. 1(a, b)에서 볼 수 있듯이 결정립 성장이 억제된 미세구조가 관찰되었다. 1,085 °C 소결체[Fig. 1(c)]의 경우 비정상 결정립 성장이 일어나 일부 영역에서 수십 µm크기의 결정립들이 관찰되었으며, matrix 결정립 성장은 여전히 억제된 것으로 확인되었다. 1,100 °C 소결체[Fig. 1(d)]는 주로 30~50 µm크기의 비정상 결정립들로 구성된 미세구조를 나타내었으며, 비정상 결정립들 사이에 수백 nm~수 µm 크기의 작은 결정립들이 관찰되었다. 반면, 1,115 °C 소결체의 경우 Fig. 1(e)에서처럼 소결 온도가 더욱 높아졌음에도 불구하고 비정상 결정립의 크기가 20 µm 수준으로 1,100 °C 소결체에 비해 감소하였으며, 비정상 결정립을 제외한 matrix결정립들의 크기는 수 µm 수준으로 관찰되었다. Fig. 1(f)는 소결 온도에 따른 소결체의 상대 밀도를 나타낸다. 전체적으로 결정립 성장이 억제된 1,055 °C와 1,070 °C에서 소결된 시편들의 경우 73 % 이하의 낮은 상대 밀도를 보인 반면, 비정상 결정립 성장이 나타나기 시작한 1,085 °C와 1,100 °C에서 소결된 시편들은 84 % 이상의 증가된 상대 밀도를 나타내었다. 하지만, 1,115 °C 소결체의 경우 가장 높은 온도에서 소결되었음에도 불구하고 1,085 °C 및 1,100 °C 소결체보다 상대 밀도가 소폭 감소하였다. Fig. 1의 결과를 통해 소결 온도의 변화에 따라 KNNS-BNKZ 세라믹스의 미세구조와 밀도 특성이 크게 달라질 수 있음이 확인되었다.
Fig. 2(a-d)는 one-step 소결체들의 XRD 결정구조 분석 결과를 나타낸다. Fig. 2(a)에서처럼 모든 소결 시편들은 이차상 없는 순수한 페로브스카이트 구조를 나타내었다. 확대된 페로브스카이트 (200)C 피크를 관찰해본 결과[Fig. 2(b)], 결정립 성장이 억제된 1,055 °C와 1,070 °C 소결체들은 단일 (200)C 피크를 나타낸 반면, 비정상 입성장과 함께 수십 µm 크기의 결정립들이 관찰된 1,085~1,115 °C 소결체에서는 (200)C 피크의 분리가 나타났다. 이 (200)C 피크의 로렌츠 커브에 의한 deconvolution fitting 결과, Fig. 2(c)에서처럼 KNNS-BNKZ 세라믹스에 rhombohedral (R)과 tetragoanl (T) 상들이 공존하고 있음이 확인되었으며, T상의 분율은 1,085 °C 소결체: 63.5 %, 1,100 °C 소결체: 91.6 %, 1,115 °C 소결체: 84.3 %로 나타났다[Fig. 2(d)]. Fig. 2(e)에 다양한 온도에서 소결된 one-step 소결체들의 압전 및 유전특성을 나타내었다. 결정립 성장이 전체적으로 억제된 1,055 °C, 1,070 °C 소결체들과 일부 비정상 결정립들이 존재하지만 matrix 결정립들의 성장은 억제된 1,085 °C 소결체의 유전손실(tanδ)은 7~15 % 정도로 높게 측정되었으나, 전체적으로 수십 µm 크기의 결정립들이 관찰된 1,100 °C, 1,115 °C 소결체들은 5 % 이하로 매우 낮아진 유전손실을 나타내었다. 유전상수는 소결 온도의 증가에 따라 크게 증가하는 경향을 나타내었다. 압전전하상수(d33) 역시 소결 온도에 따라 매우 급격하게 증가하여 1,100 °C 소결체에서 506 pC/N으로 가장 높게 나타났고 1,115 °C 소결체에서 450 pC/N으로 다시 소폭 감소하였다.

Fig. 2.
(a) X-ray diffraction patterns of KNNS-BNKZ ceramics sintered at various temperatures. (b) Partially enlarged view of XRD (200)C peaks. (c) Deconvoluted XRD (200)C peaks. (d) Rhombohedral and tetragonal phase fraction and (e) piezoelectric and dielectric properties of KNNS-BNKZ ceramics as a function of sintering temperature.
1,085 °C 소결체와 1,100 °C 소결체의 상대밀도는 84 % 정도로 유사한 반면[Fig. 1(f)], 압전전하상수는 1,100 °C 소결체에서 1,085 °C 소결체보다 4배 이상 높은 값이 측정되었다. 이는 1,085 °C 소결체에 일부 수십 µm 크기의 비정상 결정립들이 존재하지만 대다수의 matrix 결정립들의 성장이 억제되었기 때문으로 해석할 수 있다.32) 또한, R-T 상공존 조성에서 분극 공정 이후 R상의 분율이 급격하게 증가하는 현상이 보고되었으며,49) 이로 인해 T상의 분율이 80 % 이상인 조성에서 높은 압전특성이 나타난다고 보고되었다.50,51,52)Fig. 2(d)의 결과를 고려하면, 1,085 °C 소결체의 상대적으로 낮은 T상 분율 또한 낮은 압전상수의 원인으로 해석된다. 1,115 °C 소결체가 결정립 성장이 잘 일어난 미세구조와 82 % 수준의 상대밀도를 가짐에도 1,100 °C 소결체에 비해 소폭 감소된 압전상수를 나타낸 이유도 T상 분율의 감소 때문으로 볼 수 있다.
KNNS-BNKZ 세라믹스를 one-step 소결한 경우, 소결 온도 증가를 통해 비정상 결정립 성장의 촉진, T상 분율의 증가, 그로 인한 압전 및 유전 특성의 향상이 가능하였다. 하지만, 소결체의 상대밀도를 84 % 이상으로 증가시키는 것은 어려웠으며, 1,100 °C 이상의 고온 소결 시 과도한 알칼리 원소의 휘발이 그 주된 원인으로 판단된다.23,36,37,38)Fig. 3(a)는 본 연구에서 수행된 two-step 소결 조건을 나타낸다. Two-step 소결에서 1단계 유지 온도는 액상 형성 및 비정상 결정립 성장이 충분히 촉진되도록 1,130 °C로 설정되었으며, 1단계 유지 시간은 과도한 알칼리 원소의 휘발을 방지하기 위해 30분(two-step #1) 및 60분(two-step #2)으로 제한하였다. 2단계 소결 온도는 알칼리 원소의 휘발이 억제되면서 미세구조의 치밀화가 진행되도록 1,070 °C로 설정되었으며, 2단계 소결 시간은 one-step 공정과 동일하게 4시간으로 설정되었다.
Fig. 3(b-d)는 one-step (1,100 °C 소결) 및 two-step 공정으로 소결된 KNNS-BNKZ 세라믹스의 표면 SEM 이미지를 나타낸다. 전체적으로 결정립 성장이 억제되었던 one-step 1,070 °C 소결체[Fig. 1(b)]와는 달리 two-step 소결체들에서는 one-step 1,100 °C 소결체와 유사한 크기의 비정상 결정립들이 성장되었음을 확인할 수 있으며, 1단계 유지 시간이 증가할수록 비정상 결정립들의 함량이 증가됨을 볼 수 있다. 이는 고온의 1단계 공정에서 비정상 결정립들의 핵생성 양이 1단계 유지 시간에 크게 의존함을 시사하며, one-step 공정에서 가장 높은 압전 특성을 나타내었던 1,100 °C 소결체와 유사한 미세구조를 확보하기 위해서는 60분의 1단계 유지 시간이 적합한 것으로 판단된다. 비정상 결정립 성장의 유도와 더불어 더욱 주목할 점은 two-step 소결체들의 상대밀도 증가이다. One-step 1,100 °C 소결체의 미세구조에서 관찰되는 수많은 기공들이 two-step 소결 시 확연하게 감소된 것을 볼 수 있으며, two-step #1 시편과 two-step #2 시편은 각각 95 %와 96 %의 높은 상대밀도를 나타내었다. One-step 1,070 °C 소결체의 상대밀도 72 %와 비교하면, 고온 1단계 유지 공정에서 효과적으로 액상 형성이 진행되었음을 예측할 수 있다. One-step 1,100 °C 소결체의 경우, 매우 빠른 비정상 결정립들의 성장과 함께 matrix 결정립들도 수 µm 크기로 성장함에 따라 기공의 형성이 불가피하고 치밀화가 어려웠던 것으로 보인다. 반면, two-step 소결체들의 matrix 결정립들은 one-step 1,100 °C 소결체에 비해 성장이 많이 억제된 것을 볼 수 있으며, 1,070 °C의 상대적으로 낮은 2단계 소결 온도로 인해 비정상 결정립들의 성장 속도가 one-step 1,100 °C 소결체보다는 다소 감소되었을 것으로 생각된다. 1,130 °C의 고온 1단계 유지를 통해 촉진된 액상 형성과 비정상 결정립 핵생성, 그리고 1,070 °C 2단계 소결 과정에서의 낮아진 비정상 결정립 성장 속도와 matrix 결정립들의 성장 억제가 two-step 소결체들의 미세구조 치밀화 및 밀도 향상에 기여한 것으로 판단된다.
Two-step 소결체들과 one-step 1,100 °C 소결체의 XRD 분석 결과를 Fig. 4(a, b)에 나타내었다. (200)C 피크 분리를 통한 상 분율을 분석한 결과, two-step #1, #2 시편들의 T상 분율은 각각 80.08 %, 85.38 %로 나타났으며 one-step 1,100 °C 소결체의 T상 분율보다 감소된 것을 볼 수 있다. 이는 성장이 억제된 matrix 결정립들의 함량이 증가할수록(또는 결정립 성장이 억제될수록) T상의 분율이 감소됨을 시사하며, 앞선 Figs. 1, 2, 3의 결과 또한 이를 입증한다. 본 연구에서 얻어진 one-step 소결체들과 two-step 소결체들의 밀도, 압전 및 유전 특성을 Fig. 4(c)에 나타내었다. Two-step 소결 공정이 높은 밀도와 우수한 압전 및 유전 특성을 모두 확보하는데 효과적임을 확인할 수 있다. T상 분율이 one-step 1,100 °C 소결체에 비해 더 낮은 two-step #2 시편이 d33 = 574 pC/N의 가장 높은 압전전하상수 값을 나타내었으며, 소결 밀도의 증가가 우수한 압전 성능 확보에 매우 중요함을 확인할 수 있다. 압전전하상수와 더불어 중요한 압전성능 지표인 전기기계결합계수(kp) 또한 one-step 1,100 °C: 0.37에서 two-step #2: 0.50으로 35 % 이상 향상되었으며, 이는 소결체의 밀도가 압전 세라믹스의 전기기계 변환 효율에도 큰 영향을 미침을 의미한다.
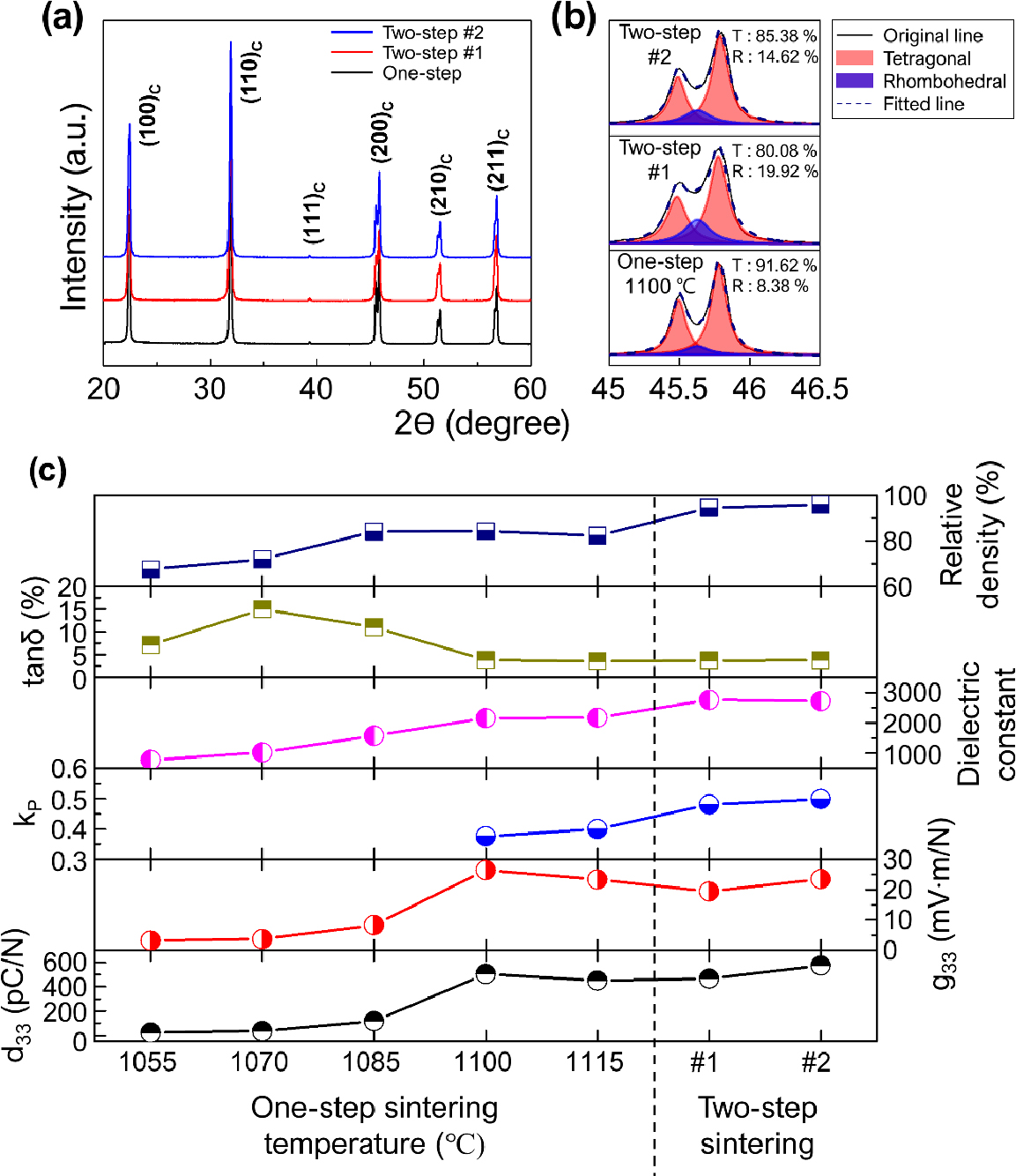
Fig. 4.
(a) X-ray diffraction patterns of KNNS-BNKZ ceramics sintered by one-step and two-step processes. (b) Partially enlarged view of XRD (200)C peaks with phase deconvolution results. (c) Relative density, piezoelectric and dielectric properties of KNNS-BNKZ ceramics sintered by one-step and two-step processes.
앞서 기술한 KNNS-BNKZ 세라믹스의 소결 공정 제어를 통한 밀도 및 압전 특성 향상이 압전 소자의 성능에 미치는 영향을 확인하고자 Fig. 5에 나타낸 것처럼 압전-자왜 적층 복합체 소자를 제작하여 자기전기 변환 성능을 평가하였다. 자기전기 변환 성능의 주요 지표인 자기전기 전압계수(α)는 다음과 같이 표현된다.53,54)
식 (1)에서 EAC는 출력되는 전기장의 세기, HAC는 인가되는 교류 자기장의 세기, n은 자왜층의 부피분율, g는 압전전압계수, q는 압전자기계수, SE와 SH는 압전층과 자왜층의 탄성 컴플라이언스, k는 압전층의 전기기계결합계수, tanδ는 유전손실, tanθ는 압전손실, C는 주파수에 따른 캐패시턴스, 그리고 Cf는 공진의 영향을 받지않는 대역에서의 캐패시턴스를 의미한다. 압전-자왜 자기전기 복합체는 one-step 1,100 °C, two-step #1, 및 two-step #2소결체를 사용하여 Fig. 5(a)에 나타낸 구조로 제작되었으며, α의 측정은 Fig. 5(b)의 장치 구성을 통해 수행되었다.
DC 자기장 세기(HDC)에 따른 자기전기 복합체 소자들의 α값을 Fig. 5(c)에 나타내었다. One-step 1,100 °C, two-step #1, 및 two-step #2소결체로 구성된 자기전기 복합체 소자의 최대 α값은 각각 306.95, 341.68, 및 456.11 mV/(Oe ‧ cm)로 측정되었다. 식 (1)을 고려하면, 높은 압전전압계수(g33)와 높은 전기기계결합계수(kp), 그리고 낮은 유전손실(tanδ)이 높은 α값 확보에 중요함을 알 수 있다. Fig. 4(c)에서 볼 수 있듯이, g33 값의 크기는 one-step 1,100 °C 소결체(26.51 mV ‧ m/N) > two-step #2 소결체(23.53 mV ‧ m/N) > two-step #1 소결체(19.43 mV ‧ m/N) 순서로 높게 측정되었으며, tanδ는 세 시편 모두 비슷한 값을 나타내었다. 따라서, 가장 높은 압전전압계수를 보인 one-step 1,100 °C 소결체로 구성된 자기전기 소자의 α값이 가장 낮게 측정된 이유는 상대적으로 낮은 소결 밀도로 인한 낮은 전기기계결합계수 때문인 것으로 해석된다.

Fig. 5.
Schematic diagrams: (a) configuration of the piezoelectric-magnetostrictive laminate composite and (b) magnetoelectric voltage coefficient evaluation system. (c) Magnetoelectric voltage coefficient (α) of the piezoelectric-magnetostrictive laminate specimens as a function of DC magnetic field (HDC) measured under 1 kHz AC magnetic field (HAC).
4. 결 론
본 연구에서는 상온에서 R-T 상경계 조성을 갖는 KNNS-BNKZ 세라믹스의 one-step 및 two-step 소결 공정에 따른 미세구조와 압전특성의 변화를 관찰하고, 소결체의 밀도와 압전특성이 자기전기 복합체 소자의 성능에 미치는 영향을 살펴보았다. One-step 소결의 경우, 1,085 °C 이상의 소결 온도에서 거대한 비정상 결정립 성장이 확인되었다. 소결 온도 증가에 따라 압전 및 유전특성이 증가하여 one-step 1,100 °C 소결체에서 506 pC/N의 높은 압전전하상수(d33) 값이 측정되었지만, one-step 1,115 °C 소결체는 소폭 감소된 450 pC/N의 d33 값을 나타내었으며, 높은 T상의 분율이 높은 압전특성 확보에 중요함을 보여주었다. 하지만, one-step 소결에서는 1,100 °C 이상의 고온에서 소결된 시편의 상대 밀도가 84 % 수준이었으며 그 이상의 상대 밀도 확보는 어려웠다. 반면, two-step 소결 공정은 KNNS-BNKZ 세라믹스의 상대 밀도를 96 %까지 크게 향상시키는데 매우 효과적이었다. 1단계 고온 유지 공정에서의 액상 및 비정상 결정립 핵생성과 2단계 저온 소결 공정에서의 낮아진 결정립 성장속도로 인한 미세구조 치밀화가 소결체의 밀도 향상에 주요했던 것으로 판단된다. Two-step 소결 공정 시 1단계 고온 유지 시간에 따라 비정상 결정립 핵생성 양이 제어되고 그에 따라 최종 미세구조가 제어될 수 있음을 확인하였다. One-step 1,100 °C 소결체에 비해 낮은 T상 분율을 가짐에도 two-step 소결체는 높은 상대 밀도로 인해 574 pC/N의 매우 높은 d33 값을 나타내었으며, 전기-기계 변환효율 지표인 전기기계결합계수(kp) 또한 one-step 1,100 °C 소결체보다 35 % 이상 향상되었다. One-step 1,100 °C 소결체 및 two-step 소결체들을 사용하여 제작된 자기전기 복합체 소자의 자기장-전기장 변환 성능을 평가해본 결과, one-step 1,100 °C 소결체가 더 높은 압전전압계수(g33) 값을 가짐에도 낮은 kp로 인해 가장 낮은 자기전기 전압계수(α) 값을 나타내었다. 이 결과들은 KNNS-BNKZ 세라믹스의 높은 T상 분율과 높은 상대 밀도 확보가 압전 소재 및 소자 성능 향상에 필수적이며, two-step 소결 공정이 고 휘발성 원소를 포함한 세라믹 소재의 미세구조 제어에 매우 효과적임을 보여준다.