1. 서 론
리튬 이차 전지(lithium-ion battery)는 노트북, 스마트폰 등 에너지 집약적인 휴대용 기기의 전력원으로서 자리매김하고 있다. 리튬 이차 전지의 성능 향상에 있어서 고에너지 밀도 및 사이클 수명의 안정성은 고려해야 할 주요 요소이며 이러한 특성들은 전극 소재의 개발을 통해 향상될 수 있다.1,2) 현재 리튬 이차 전지 음극 소재로서 상용되고 있는 graphite는 저렴한 가격, 우수한 수명 안정성의 장점을 가지지만 372 mAh/g의 낮은 이론 용량, 낮은 율속 특성의 문제로 인해 고용량 음극 소재의 개발 필요성이 대두되고 있다.
실리콘(silicon, Si)은 기존 탄소(carbon, C)계 소재보다 약 10배 가량 높은 4,200 mAh/g의 이론 용량을 가지고 있으며 작동 전압이 낮아 에너지 밀도가 높은 배터리의 설계에 유리하다.3) 또한 매장량이 풍부한 친환경 물질이라는 특성으로 인해 리튬 이차 전지의 차세대 음극 소재로서 각광 받고 있다.4) 그러나 실리콘은 리튬 이온과 alloying/de-alloying 반응 시 400 %에 달하는 큰 부피 팽창으로 인한 활물질의 파쇄가 발생하게 되고 또한 solid electrolyte interphase (SEI) layer의 지속 형성에 따른 높은 저항 형성 및 급격한 용량 저하를 초래한다는 문제가 여전히 남아있다.5) 이러한 부피 팽창 문제를 개선하기 위한 방안으로 실리콘의 입자 크기 및 형상 제어를 통한 부피 팽창 감소에 관한 연구가 활발히 진행되고 있으며 다공성 실리콘 입자의 용량 유지 특성이 Si/C 복합 재료 및 실리콘 나노입자보다 우수하다는 연구 결과가 보고된 바 있다.6,7) 이러한 연구결과를 토대로 다공성 실리콘을 제조하여, 리튬 이온의 빠른 이동성의 유도 및 입자 내부에 형성된 중공의 buffer layer 역할을 통해 실리콘 부피 팽창 완화를 예상할 수 있다.8) 현재 3차원 다공성 나노 실리콘을 합성하기 위한 대표적 방법으로는 metal-assisted chemical etching (MACE)가 있으며, MACE법으로 합성된 다공성 실리콘은 높은 탭 밀도와 크기로 인해 높은 초기 효율을 보인다.9)
본 연구에서는 이러한 고용량 실리콘의 부피 팽창에 따른 문제점들을 해결하기 위하여, MACE 법을 활용한 다공성 실리콘 입자를 제조한 후 etching 시간에 따른 다공성 실리콘 특성 차이를 비교하였다. 추가적으로, 고가의 실리콘을 남용하는 대신 공정 진행 후 남은 Si wafer 슬러지를 활용하여 공정 원가 절감에 기여하였다. 이는 향후에 Si wafer 슬러지로 인한 환경 문제 감소에도 영향을 끼칠 것이다.10)
2. 실험 방법
2.1. 나노 실리콘 분말 제작
저항이 10 Ω cm인 P-type Si<100> 웨이퍼를 600 rpm으로 12 h 동안 ball mill하였다. 이때 zirconia ball 10 mm 100 g을 사용했다.
2.2. 다공성 실리콘 분말 제작
MACE 공정으로 다공성 실리콘 분말을 제작하였다. Ag입자 증착을 위해 7.26 M HF, 0.017 M AgNO3 용액에 나노 실리콘 분말을 넣고 마그네틱 바로 1 min 30 s 동안 stirring하였다. 이후, deionized (D.I) water안에 10 min 동안 안정화단계를 거쳤다. 그리고 7.26 M HF, 0.50 M H2O2 용액에 Ag입자를 증착한 나노 실리콘 분말을 넣고 각각 1 min, 5 min 동안 식각하였고, HNO3 수용액(70 %)와 D.I water를 2:1 vol%로 혼합한 용액을 Ag입자가 증착된 나노 실리콘 분말 위에 천천히 부었다. 수득된 분말은 D.I water로 세척하고 최종 분말을 수득했다.
2.3. 셀 제작 및 전기화학적 특성 분석
제조된 다공성 실리콘 활물질의 전기화학적 특성을 확인하기 위해 Li foil을 상대전극으로 한 하프 코인셀을 제조하였다. 활물질로 각각 나노 실리콘 분말, 1 min와 5 min 동안 식각한 다공성 실리콘 분말을 사용하였다. 활물질, 도전재(super P)와 바인더(25 wt% polyacrylic acid)를 6:2:2의 중량비로 하였으며 mass loading은 0.6~0.7 mg/cm2로 제작하였다. Mixer를 이용하여 2,000 rpm으로 8 min 동안 mixing하고, 2,200 rpm으로 30 s 동안 degas하였다. 그 다음으로 집전체로 10 µm구리 호일을 사용하고 전체 두께는 50 µm가 되도록 casting하였고 진공오븐에서 85 °C에서 4 h 동안 건조하였다. 이후 14 π 크기로 전극을 제작하였으며 분리막(celgard 2400 polyprophylene)은 20 π를 사용하여 셀을 조립하였다.
제조된 다공성 실리콘 분말의 표면을 scanning electron microscope (SEM)을 통해 확인하였다. 기타 불순물 확인과 미세화 확인을 X-ray diffraction (XRD)을 통해 하였으며 Brunauer-Emmett-Teller (BET)를 통해 다공성 실리콘 분말의 표면적과 기공에 대한 분석을 실시하였다. 또한, 분말의 나노스케일 크기 차이를 확인하기 위해 dynamic light scattering (DLS)을 실시하였다. 제작된 전지의 전기화학적 특성을 평가하기 위해 Land CT2001A system을 사용하여 1 C의 C-rate로 사이클 측정을 했으며 cyclic voltammetry (CV)를 0.01~1.5 V의 potential range, 0.1 mV/s의 scan rate로 측정하였다.
3. 결과 및 고찰
다음 Fig. 1에 실리콘 분말 제작 메커니즘을 나타내었다. 실험 과정에서 식각 공정을 마친 샘플의 Ag particle을 제거하기 위해 사용한 질산에 의해 실리콘은 질산에 담갔을 때 수 nm 단위의 얇은 SiO2가 생성됨10)과 동시에 Ag가 식각한 자리는 pore의 형태로 남게 된다. 이러한 pore의 형태를 따라 전체적인 표면에 얇은 SiO2가 생기며 이는 실리콘의 core의 부피가 팽창하는 것을 막아주는 core shell로서의 역할을 한다.11) 이때 식각 시간이 증가함에 따라 실리콘 분말의 크기가 줄어듦과 동시에 생성된 pore의 비표면적 또한 증가하게 된다. 이는 pore부분의 산화막의 비표면적도 함께 증가함을 의미한다. 그러므로 실리콘의 내부의 팽창으로 인한 파괴를 더욱 억제할 수 있게 된다.
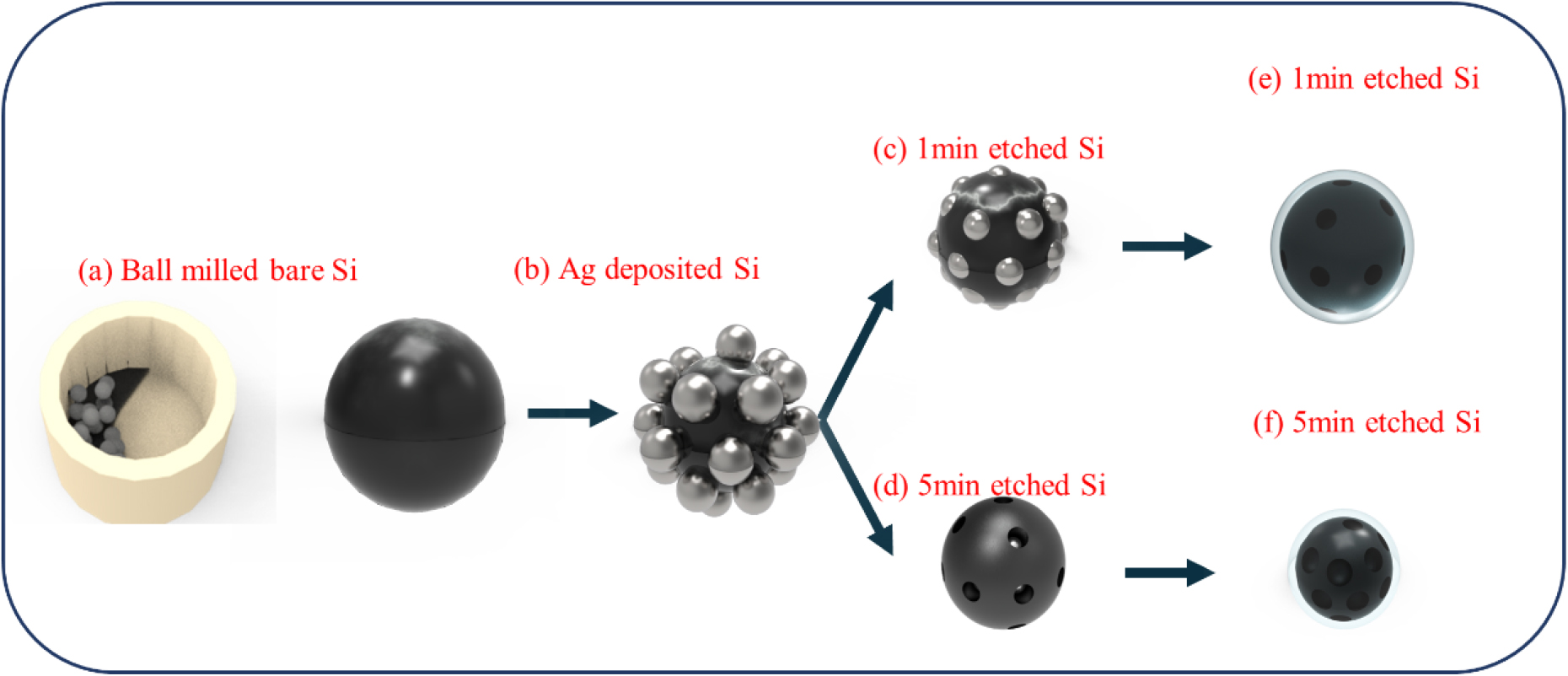
Fig. 1.
Schematic of the fabrication procedure for porous Si powder (a) Bare Si after ball milling, (b) Ag deposited Si powder (c) 1 min etched Si powder, (d) 5 min etched Si powder. (e) 1 min etched Si powder’s after Ag removal by HNO3 Si particle, (f) 5 min etched Si powder’s after Ag removal by HNO3.
분말의 나노스케일 크기 차이를 확인하기 위해 DLS 분석을 시행한 결과를 Fig. 2에 나타내었으며 각 분말의 평균 지름을 Table 1에 나타내었다. Fig. 2(a)는 ball mill 공정을 거친 bare 실리콘 분말, Fig. 2(b)는 MACE 공정에서 식각 단계를 1 min 동안 거친 실리콘 분말, 그리고 Fig. 2(c)는 식각 단계를 5 min 거친 실리콘 분말이다. DLS 분석 결과, bare Si powder의 경우 평균 지름이 121.2 nm로 가장 크며 1 min 동안 식각한 샘플, 5 min 동안 식각한 샘플의 평균 지름이 각각 118.1 nm, 66.9 nm로 5 min 동안 식각을 진행한 샘플에서 더 작은 나노스케일 실리콘 분말의 분포가 증가함을 확인할 수 있었다. 이때의 반응식 (1), (2), (3), (4)를 아래에 나타내었다.12)
이때 식각 시간이 증가될수록 기공은 더욱 깊게 형성됨과 동시에 입자 크기도 감소하기 때문에 실리콘 분말의 나노화가 진행되어 실리콘 분말의 지름이 감소한 것으로 예상한다. 또한, 식각이 진행되며 Ag 이온은 Ag film 근처에 가장 많이 생성되기 때문에 실리콘에 생긴 다공성 구조에서 측벽 방향으로도 Ag 입자가 환원되어 재생성 되며 또 다른 다공성 구조를 형성시킨다.13,14,15 따라서 이 역시 실리콘 분말의 미세화 및 기공형성을 촉진시켰을 것으로 예상한다.
Table 1.
Average Si powder’s diameter
Average diameter (nm) | |
Bare Si powder | 121.2 |
1 min etched Si powder | 118.1 |
5 min etched Si powder | 66.9 |
실리콘 분말의 표면에 불순물 확인과 미세화 확인을 위해 XRD 분석을 실시하여 Fig. 3에 도시하였다. Fig. 3의 모든 데이터에서 2θ = 28°, 47°, 56°에서 회절 피크를 확인할 수 있다. 이는 실리콘 분말의 X-선 회절 피크(JCPDS 27-1402)에 해당하며 실리콘 결정면인 (111), (220), (311), (400), (331)과 일치한다.16) 따라서 Ag 입자가 잘 제거되었으며 다른 불순물이 존재하지 않음을 나타낸다. Fig. 3의 intensity를 각 샘플 별로 비교하였을 때, bare Si powder의 피크보다 1 min etching Si powder, 5 min etching Si powder 순서대로 intensity의 반가폭(full width at half maximum, FWHM)이 각각 0.21°, 0.39°, 0.51°로 점점 broad해지는 변화가 나타난다. 이는 입도 미세화와 동시에 내부 혹은 경계면의 변형이 많을수록 회절 피크에 영향을 더 많이 미치기 때문에 나타나는 변화이다.17),18)
Bare Si powder의 입도 변화를 확인하기 위해 아래의 Scherrer 공식 (5)로 결정 크기를 계산하였다.19)
L은 평균 결정 크기, λ는 Cu target의 X-선 파장 값인 0.15406 nm, FWHM은 반가폭, θ는 main peak 면에서의 산란각이다. 다공성 구조를 형성시킨 샘플의 경우, 격자 변형으로 인한 피크 확장을 위한 구성요소를 도입한 Scherrer 방정식을 재배열한 공식 (6)으로 결정 크기를 계산하였다.
B는 FWHM, θ는 main peak 면에서의 산란각, λ는 Cu target의 X-선 파장값인 0.15406 nm, d는 평균 결정 크기, η는 lattice strain, K는 Scherrer constant로, 1로 설정하였다. 각 평균 결정 크기는 0.76 nm, 0.41 nm, 0.31 nm로 계산된다. 따라서 Fig. 1에서 DLS 분석 결과와 함께 확인하였을 때 5 min의 etching time에서 더 작은 나노스케일 분포가 증가함을 알 수 있다.
시료 표면의 pore 특성을 확인하기 위하여 BJH (Barrett-Joyner-Halenda model) 방식으로 측정한 Fig. 4(a)에 pore size distribution curve를 나타내었다. 식각 시간이 더 긴 5 min etched Si powder 샘플에서 diameter가 30 nm 이상의 pore가 증가함을 보이며, 동시에 그 이하의 pore diameter는 줄어듦을 보였다. Ag MACE는 대부분 10 nm이하의 Ag particle로 식각을 하지만, 이보다 큰 pore diameter가 30 nm이상인 pore들이 점차 증가하는 현상을 보인다.20),21) 이는 식각 시간이 증가함에 따라 10 nm 이하의 깊은 pore들이 식각을 진행하며 pore가 통합되는 현상이 30 nm 이상의 pore를 형성하였을 것으로 판단한다. 이 과정에서 탈락되는 Si particle은 식각 용액에 의해 제거된다. 이러한 Si particle의 탈락 현상은 pore의 비표면적 감소를 야기시킬 수 있다. N2 가스가 adsorption-desorption되는 isotherms인 Fig. 4(b, c)를 비교하였을 때, 다공성 흡 ‧ 탈착의 개형이 비슷하므로 pore size 분포의 비율은 유사하다. 하지만, 1 min, 5 min etched Si powder의 surface area는 각각 60.5, 46.0 m2/g로 감소가 나타났다. 이는 Fig. 4(a)에서 5 min etched Si powder에서 meso (2~50 nm)단위의 pore가 더 많이 존재하기 때문이다. 또한, pore의 통합을 통한 pore의 확장은 surface area의 감소로 인했을 것으로 판단한다. 즉, meso에서 macro 단위의 pore로 변했으므로 비표면적의 감소를 의미한다. 이때 표면에 얕게 발생한 다수의 pore에 비하여 소수의 깊은 pore는 pore volume이 더 클 것이다. 따라서 실리콘 분말이 충방전시 부피 팽창에 대한 여유 공간으로서 더욱 잘 작동할 수 있을 것으로 예상한다.
다공성 실리콘의 표면 형상 및 크기를 제어하기 위한 변수로서 식각 시간을 조절하여 다공성 실리콘 분말을 제조한 후 SEM으로 분석하였다. MACE 공정을 진행하지 않은 Fig. 5(a)의 경우 비교적 매끄러운 표면 형상을 띄지만, MACE 공정을 진행한 Fig. 5(b, c)의 경우 Fig. 5(a)와 다르게, 실리콘 표면에 미세한 기공이 형성되었다. 또한, Fig. 5(c)가 Fig. 5(b)에 비해 더 거친 표면 형상을 보임을 통해 식각 시간이 증가할수록 실리콘 표면의 기공의 깊이가 깊어지고 그 수가 증가함을 알 수 있었으며, 결과적으로 실리콘의 다공성의 정도가 증가하였다. 더 많은 표면의 텍스처를 띄는 Fig. 5(c)는 리튬 이온의 효율적인 이동을 촉진하기에 전지의 전기화학적 특성에 있어 가장 긍정적인 영향을 미칠 것으로 예상된다.22)
리튬 이차 전지 음극 소재로서의 성능을 측정하기 위하여 전기화학적 분석 기법으로 충 ‧ 방전 테스트를 실시하였다. 전극 소재인 다공성 실리콘은 제조 시 식각 시간을 1 min, 5 min으로 설정하였으며 전구체인 구형의 bare Si powder와 방전 특성을 비교 분석한 데이터를 Fig. 6으로 나타내었다. 충 ‧ 방전 테스트는 0.1 C 3 cycle, 1 C 200 cycle를 순차적으로 진행하였다. Fig. 6을 통해 bare Si powder, 1 min etched Si powder, 5 min etched Si powder의 초기 용량은 각각 3,801, 3,693, 3,683 mAh/g으로 유사한 값을 가졌다. 또한, 100 cycle의 용량 및 용량 유지율(%)은 각각 1,139 (30 %), 1,302 (35 %), 1,400 (38 %) mAh/g으로 식각 시간이 늘어날수록 용량 유지율(%) 및 사이클 안정성이 증가하는 경향을 보였다. 이는 식각 시간이 길어질수록 다공성 실리콘의 비표면적이 늘어나 전극과 전해액 간의 접촉 면적이 증가하게 됨으로써 이온의 빠른 이동성을 유도하게 되고, 실리콘 입자 내부에 형성된 중공은 buffer 역할을 수행함으로써 충 ‧ 방전 과정 중 발생하는 부피 변화율의 감소와 전극 형상 유지에 기여한 것으로 판단된다.19) 입자 크기의 나노화로 인해 리튬 이온의 확산 거리를 단축시키고, 리튬 이온의 alloying/de-alloying 속도를 증가시킴으로써, 실리콘의 부피 변화율 감소에 추가적으로 기여함을 확인하였다.
샘플의 가역적 리튬 저장 성능은 Li foil을 상대전극으로 한 하프 코인셀을 제조하여 평가되었다. 방전(리튬화) 및 충전(탈리튬화) 과정 동안의 산화환원 반응을 나타내기 위해 다공성 실리콘 분말의 CV 측정을 처음 3주기 동안 기록하였다. Fig. 7(a)에서 첫 번째 방전 과정(음극 스캔) 동안 0.16 V에서 피크가 나타나며, 이는 bare Si powder와 리튬의 반응을 통해 비정질 LixSi가 형성됨을 나타낸다.23,24,25) 충전 과정(양극 스캔) 동안에는 0.6 V의 넓은 피크와 0.3 V의 작은 피크가 관찰되며, 이는 LixSi가 다시 실리콘으로 dealloying 됨을 의미한다.26)Fig. 7(a, b) 모두 방전과 충전 과정에서 같은 위치에 피크가 나타나며, 이는 Si의 일관된 리튬화(음극) 및 탈리튬화(양극) 과정을 보여준다. Fig. 7(b)는 Fig. 7(a)에 비해 더 높고 날카로운 형태의 피크를 나타내는데, 이는 리튬 이온의 확산이 촉진되고 전극 내부 저항이 감소했음을 의미한다. 또한, 다공성 구조로 인해 표면적이 증가함에 따라 전해질과의 접촉 면적이 증가하여 리튬 이온의 삽입과 탈리 과정이 더욱 용이해진 것에 기인한다.
4. 결 론
본 연구는 리튬 이차 전지 음극재로 실리콘의 안정성을 향상하기 위하여 MACE 공정을 이용하여 식각 시간을 조절한 다공성 실리콘 분말을 제조하였으며 최종적으로 5 min etched Si powder 샘플이 bare Si powder샘플에 비해 안정성이 향상된 음극재를 얻었다.
식각 시간을 다르게 설정한 다공성 실리콘 분말의 XRD 분석 결과, 평균 결정 크기가 5 min 동안 식각을 진행한 샘플에서 더 작아졌으며 DLS 분석 결과 입자 평균 지름이 5 min etched Si powder 샘플에서 더 작아져, 나노화가 진행됨을 보였다. SEM을 통해 입자의 다공성 구조를 확인한 결과, 식각을 진행한 샘플에서 Ag입자가 Si표면을 파고들어가 다공성 구조를 형성함을 확인하였다.
전기화학적 특성을 평가하기 위해 cycle과 x평가를 진행하였으며, 확인한 결과 용량 유지율이 bare Si powder에 비해 8 %가량 향상된 것을 확인할 수 있었다. 이는 5 min 동안 식각을 진행한 샘플에서 다공성 실리콘의 비표면적이 늘어나 전극과 전해액 간 접촉 면적이 증가하여 이온의 빠른 이동을 유도하게 되었기 때문이며, 입자의 나노화로 인해 리튬 이온의 확산 거리를 단축시키고 alloying/de-alloying 속도를 증가시킨 결과이다. 더불어 실리콘 입자 표면의 pore는 실리콘의 core부분과 비교하였을 때, pore의 표면에 존재하는 산화막이 하나의 shell로써 작동하며 실리콘의 부피 변화가 감소할 수 있도록 하였기 때문에 나타난 결과이다.
위의 실험 결과들을 종합하면 전지의 안전성 및 수명 특성에 대한 개선을 예상할 수 있다. 그러나 다공성 구조가 지나치게 많이 형성되는 실리콘 입자는 기계적 강도를 약화시켜 구조적 안정성이 감소될 수 있으므로 식각 시간에 따른 입자 나노화의 정도를 조절하여 최적의 조건을 찾거나 산화막의 두께를 조절하는 등의 최적의 다공성 정도를 찾는 연구가 추가적으로 수행되어야 할 것으로 판단한다.